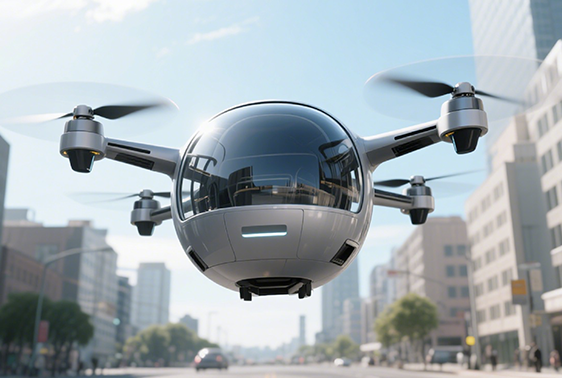
空间和载重极为敏感的商业低空飞行器而言,这无疑是一大利好,意味着在有限的机身空间内,飞行器能够获得更强大的动力输出,为实现更多复杂的飞行任务和应用场景提供了可能。
其次,轴向磁通电机扁平的外形特点使其在飞行器布局中具有无可比拟的优势。这种扁平结构能够轻松嵌入商业低空飞行器的机翼、涵道等狭小空间,不仅极大地简化了传动链,减少了能量在传输过程中的损耗,还显著提升了能量传输效率。以常见的eVTOL(电动垂直起降飞行器)为例,搭载轴向磁通电机后,动力输出可提升约20%,有效载荷得以增加,能够多搭载1-2名乘客或承载更多货物。同时,动力系统重量占比降低,为飞行器的续航争取到了更多的能源空间,有力推动了低空装备从“概念验证”向“商业运营”的实质性跨越。
面临的挑战与应对。
然而,轴向磁通电机在商业低空飞行器领域的广泛应用并非一帆风顺,仍面临着诸多技术挑战。在绕组技术方面,扁线绕组虽被视为提升电机效率的关键技术,但实际应用中却困难重重。扁线端部焊接需采用激光焊接或电阻焊接等高精工艺,以确保低接触电阻,且良品率需达到99%以上。绝缘处理也极为严苛,既要耐高温(150C-200°C)又要耐高压,传统浸漆工艺容易在扁线间隙产生气泡,降低绝缘可靠性。在散热方面,轴向磁通电机运行时内部温度常常高达150°C-200℃℃,传统钕铁硼磁材在这样的高温环境下,性能会急剧下降。一旦局部热点温度接近磁材居里温度,还会引发不可逆退磁,直接导致电机失效。而其紧凑的结构设计,使得散热成为一大难题,盘式结构导致轴向空间狭窄,传统风冷方式难以有效导热,热阻大、效率低。
尽管面临挑战,但行业内的科研人员和企业积极探索解决方案。在绕组技术上,研发高精度成型机、入槽机器人,并借助3D视觉引导将入槽误差控制在极小范围内,采用超声波焊接、真空压力浸漆(VPI)+纳米涂层技术,降低接触电阻,提升绝缘寿命。在散热方面,尝试集成环形液冷通道,采用强制循环的冷却液,以及布置相变材料(PCM)+热管,并结合智能热管理系统,来提升散热效率,降低局部热点温度。
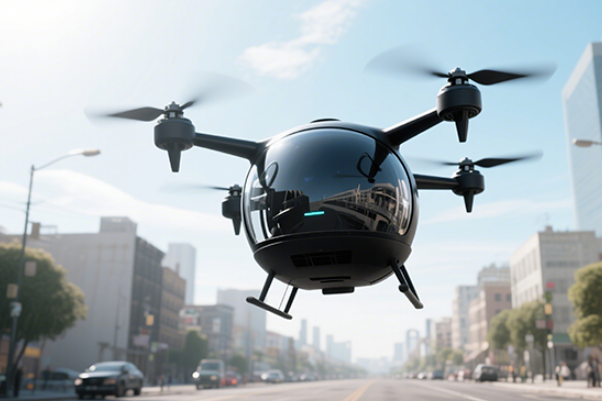